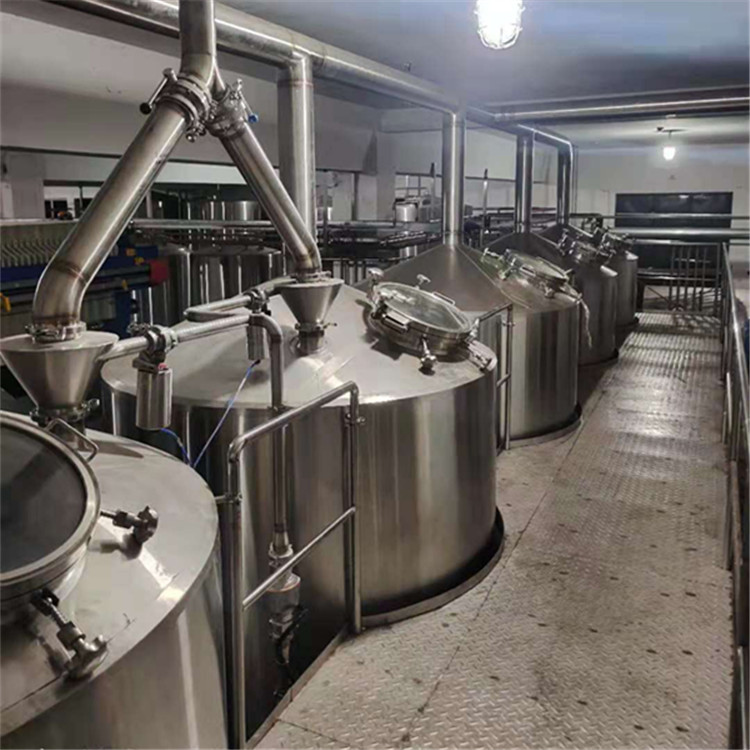
If you are planning to build a brewery, you must consider the turnkey beer project. What is the whole turnkey beer production line like? Which manufacturers can do a good job in this beer production line? What problems should we pay attention to? The beginning of a new project certainly requires a lot of preparatory work and a lot of problems. Many times, it is very difficult. This professional problem should be solved by a professional company. We can provide you with the turnkey work of the whole beer project, with more than 60 years of production experience.
Before you decide to build a beer production line, you must know something about the market, beer types, factories and other issues, and the output is also determined. Therefore, you need to tell us your local voltage and frequency, and what is your daily output? How many kinds of beer are produced? What's the budget? According to these, we will ask engineers to make the technical configuration scheme of beer production line. Today, I'd like to talk about the beer equipment production line. It doesn't represent every customer, because the needs of every customer are different. We need continuous communication and exchange.
Turnkey solution for the beer brewing production line-the materia
First of all, the determination of material has a great impact on the price. Generally, we use 304 stainless steel for the whole beer system. If customers have special requirements, 316L stainless steel can also be used, and the cost will certainly increase accordingly. Copper can also be outsourced to make it look more beautiful. Generally, food grade 304 stainless steel is OK.
Turnkey solution for the beer brewing production line-Malt milling system
For small and medium-sized beer equipment, the counter roll malt crusher is commonly used, and the output is slightly larger. Multi roll malt crusher is used. Small and medium-sized beer equipment is generally dry powder. Malt is crushed for better dissolution. The malt is broken but not broken, and the wheat peel acts as a filter for wort filtration.
This wet malt crusher is suitable for large breweries. Finally, the malt is adjusted into thicker wheat pulp, which can reduce the flying of malt dust and protect the production environment.
Turnkey solution for the beer brewing production line-Mash system
Model | Output | Combination mode | Voltage | Heating mode | Material | Scope of application | Control mode |
100L | 100L/batch | Two vessels brewhouse | 380V/220V | by steam,by electricity,by fire | SUS304/316L | Hotel、wine bar.restaurant etc. | Semi automatic / automatic |
Three vessels brewhouse | |||||||
200L | 200L/batch | Two vessels brewhouse | 380V/220V | by steam,by electricity,by fire | Hotel、wine bar.restaurant etc. | ||
Three vessels brewhouse | |||||||
500L | 500L/batch | Two vessels brewhouse | 380V/220V | by steam,by electricity,by fire | Hotel、wine bar.restaurant etc. | ||
Three vessels brewhouse | |||||||
1000L | 1000L/batch | Two vessels brewhouse | 380V/220V | by steam,by electricity,by fire | Hotel、wine bar.restaurant etc. | ||
Three vessels brewhouse | |||||||
Remark | The above models can be customized according to the requirements |
The saccharification system is the key to brewing beer. We all know that the saccharification process is inseparable from "saccharification lautering boiling whirlpool", so the combination of saccharification system evolved according to these four steps, that is, these four steps are completed by several cans. It is called two saccharification by two tanks and three saccharification by three tanks. Each function is completed by one tank, which is called four saccharification. The hot water tank is an auxiliary equipment. Therefore, the selection of several saccharifiers affects the output and processing speed. If you need to work 24 hours a day, it is recommended to choose the minimum four saccharifiers or even more.
Turnkey solution for the beer brewing production line-Fermentation system
The fermentation tank ferments the cooled wort through yeast, which converts sugar into alcohol and carbon dioxide. The number of fermentation tanks is determined according to the daily output. The fermentation tank is a cylindrical structure with a conical bottom to facilitate the precipitation of yeast. The outside is jacketed by Miller plate or coil, and the medium inside is ethylene glycol or alcohol, which is used to cool the tank, which is more conducive to yeast fermentation. With thermal insulation, the outermost layer is provided with a shell, which can be made of 304 stainless steel or carbon steel.
Turnkey solution for the beer brewing production line-Cooling system
Cooling system the main function of refrigeration system is to provide cold source for cooling wort and fermentation after swirling sedimentation. The main equipment consists of: ice water tank (add ethylene glycol or edible alcohol with 30% of the tank volume to ensure no freezing at minus 6 ℃), cold water tank (large equipment and multi batch brewing need to be equipped, small equipment can not be used) and refrigerator.
Turnkey solution for the beer brewing production line-Cleaning system
CIP system breweries generally use the cleaning in place (CIP) method to clean and sterilize the equipment, that is, the process of cleaning and disinfecting the equipment without dismantling the equipment parts or pipe fittings in a closed environment. The larger the equipment, the higher the requirements for cleaning the equipment. Configure CIP equipment according to equipment size and requirements
Configuration of turnkey solution for the beer brewing production line
Code | Name | No. | Component |
1 | Malt milling system | 1 | Malt milling machine |
2 | Mash system | 1 | Mash/kettle tun |
2 | Lauter/whirlpool tun | ||
3 | Hot liquor tank | ||
4 | Plate heat exchanger | ||
5 | Wort oxygenator | ||
6 | Yeast addition tank | ||
7 | Operation platform | ||
8 | Wort pump | ||
9 | Hot water pump | ||
3 | Fermentation system | 1 | Fermenter |
2 | Mixing tank | ||
3 | PRV | ||
4 | Vent valve | ||
4 | Cleaning system | 1 | Mobile cleaning cart |
5 | Cooling system | 1 | Chiller |
2 | Glycol water tank | ||
3 | Ice water pump | ||
6 | Electrical System | 1 | Fermentation auto control |
2 | Switchboard | ||
3 | Fermentation control solenoid valve | ||
4 | Temperature Sensor | ||
5 | Wire and Cable | ||
6 | Threading tube | ||
7 | Filling system | 1 | Bottle rinsing machine |
2 | Linear filling and capping machine | ||
3 | Linear sticker labeling machine | ||
4 | Conveyor system | ||
8 | Steam system | 1 | Electric steam boiler |
9 | Pipeline accessories | 1 | Mash, CIP, water pipeline |
2 | Glycol water pipeline | ||
3 | Steam pipeline | ||
4 | Air compression pipeline | ||
5 | Food grade hose | ||
6 | Other |
The above configuration of turnkey solution for the beer brewing production line is for reference only. Please contact us and we will design it separately according to your requirements.
If you want to ask anything just fill in the form below and send us.